The Future of Screw Jack Technology – Trends and Innovations
Screw Jacks have become an increasingly popular alternative to hydraulic systems in industrial machinery. Not only can they reduce energy costs significantly while simplifying repair operations, they are also an economical solution.
Screw jacks will remain popular choices for lifting and positioning purposes across various industries as automation and robotics take hold in global markets.
Electric Motors
Electric motors are the preferred power source for screw jacks, offering greater energy efficiency compared to hydraulic systems that must maintain constant pressure – something which can become extremely costly and time-consuming over time.
An electric motor consists of two components, the stator and rotor. Both components are composed of magnetic materials and electrical conductors that interact to generate mechanical energy through magnetic fields created by each component. The stator generates an eddy current magnetic field which interacts with that generated by its counterpart (rotor) to produce mechanical energy.
Electric motors come in various configurations, from non-salient to salient-pole designs. Salient-pole designs feature projections called poles on either end of their stator or rotor cores which face each other, with wire wrapped under each pole face acting as either the south or north pole of their respective fields as current travels through it.
Automation
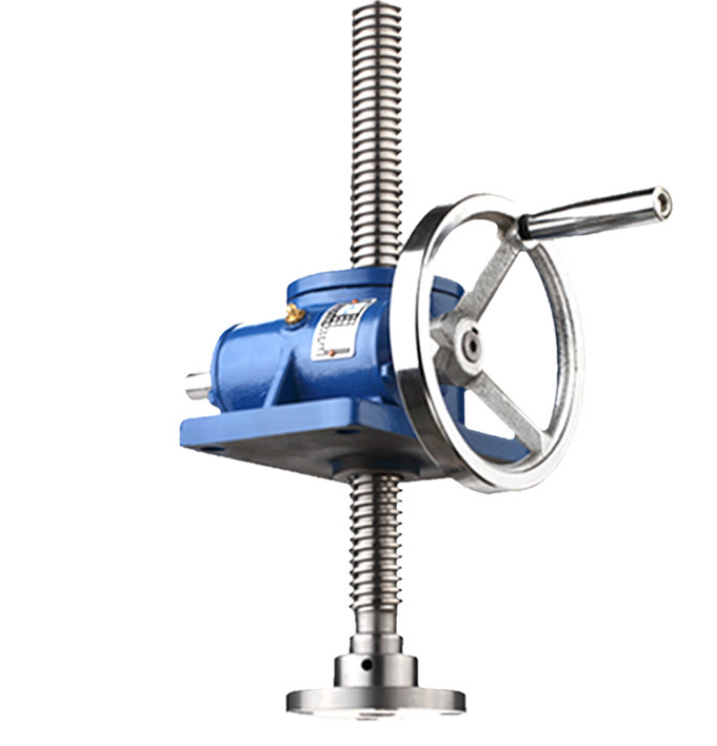
Automating repetitive tasks enables manufacturers to rapidly change production processes and develop new products with minimal human input. Furthermore, automation enables monitoring and controlling production data which helps lower costs while aiding accurate decision-making.
Automated systems can make work safer for employees, and the Occupational Safety and Health Act of 1970 encourages their use in factories. Robots and other automated devices help keep workers away from potentially hazardous situations while eliminating repetitive tasks that are error-prone when performed manually by humans.
Understanding how machine screw jacks operate and their proper mounting methods is critical in selecting an ideal screw jack for any application. These include lifting screw, gearbox and thrust-bearing load support components. Understanding their designs works and installation procedures are key steps towards choosing an ideal jack solution.
Robotics
Robotics is an exciting field that utilizes technology to build machines that perform tasks that would be impossible for humans. Such machines can assist with industrial processes, search-and-rescue missions and military operations among many other things.
Robots are composed of sensors, actuators and a brain that are controlled by programs. Sensors collect information from their environment before sending it on to the brain for evaluation and use. Once complete, this process allows the robot to do its work more effectively.
Robotics come in all shapes and sizes, from simple machines that follow preprogrammed actions to independent autonomous bots that operate completely independent from human control. Some of the biggest advantages of robotics include increased safety, reduced costs and greater accuracy.
Mechatronics
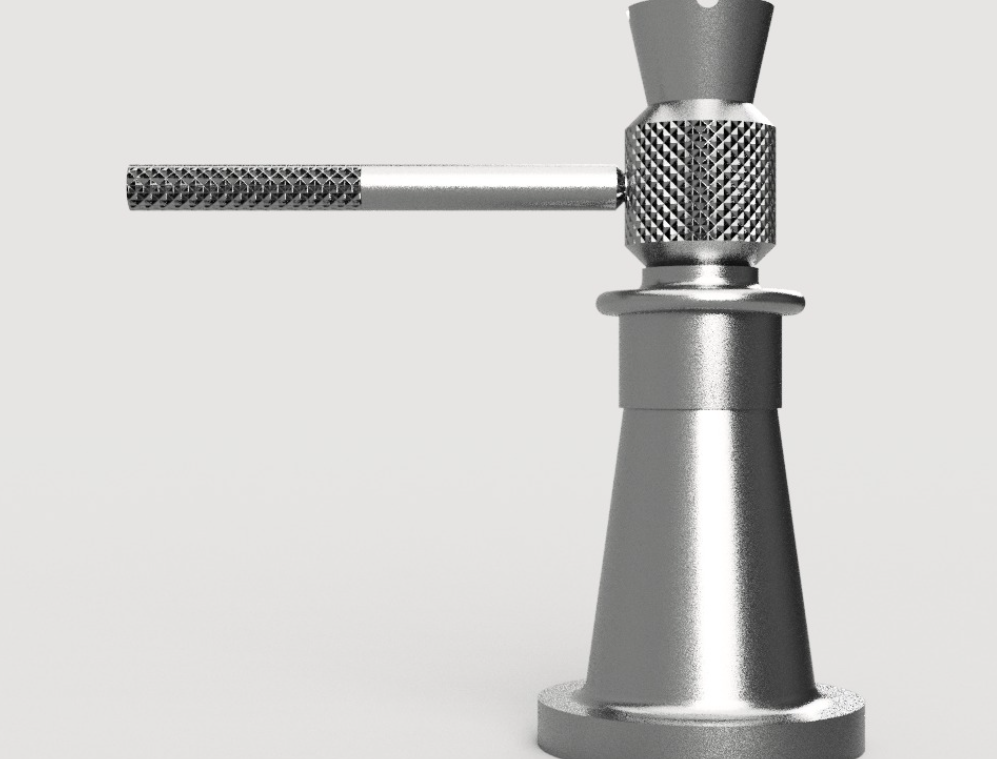
Mechatronics is an engineering discipline which examines the relationships among mechanical, electrical and electronic systems. Engineers specializing in this area may work across industries like healthcare, manufacturing and construction – among others.
Screw jack systems typically involve using high-torque AC induction motors for system design. Their size should match up with both running torque requirements for the jack as well as mounting decisions necessary to avoid column buckling.
Screw jack types become more power intensive as more components are added, such as couplings or miter boxes that increase drag on their main motors.
Mechatronics engineers can break down traditional engineering silos in order to find more efficient ways to integrate different systems, creating smaller machines that run more effectively while decreasing production costs. Furthermore, mechatronics technologies monitor mechanical systems’ performance so as to detect issues early and avoid breakdowns.